Unlocking Potential: The Role of a Plastic Prototype Manufacturer in Today’s Market
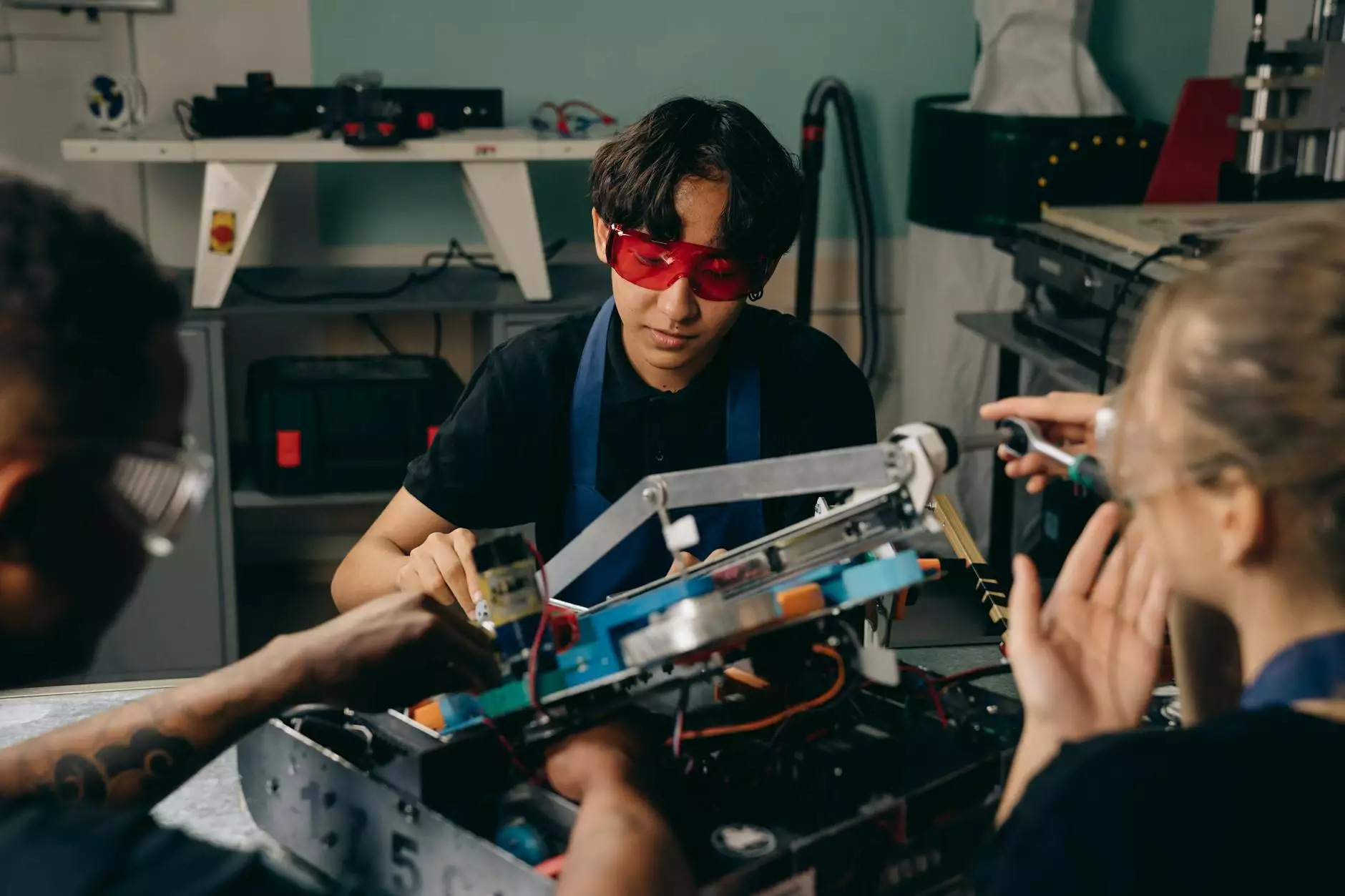
In a world where innovation drives the market, the importance of effective prototyping cannot be overstated. Plastic prototype manufacturers stand at the forefront of this revolution, providing companies with the tools needed to bring concepts to life. Whether you are developing new products or refining existing ones, understanding the benefits of engaging a dedicated manufacturer is crucial to maintaining a competitive edge.
What is a Plastic Prototype Manufacturer?
A plastic prototype manufacturer specializes in creating functional and aesthetic models from plastic materials. These prototypes serve as tangible representations of designs, enabling businesses to visualize, test, and refine their ideas before initiating full-scale production. By leveraging advanced technologies and materials, these manufacturers facilitate the rapid development and adjustment of prototypes, ensuring that designs meet both market needs and regulatory standards.
Benefits of Using a Plastic Prototype Manufacturer
1. Cost Efficiency
One of the most compelling reasons to engage a plastic prototype manufacturer is the significant cost savings it provides. Developing products without a prototype can lead to expensive errors in production. By investing in prototyping, businesses can:
- Minimize Material Waste: Prototypes reduce the likelihood of costly mistakes in mass production.
- Identify Design Flaws Early: Catching issues before they escalate avoids further expenses later in the development process.
- Enhance Resource Allocation: Efficient prototyping allows companies to allocate their resources towards successful iterations.
2. Speed to Market
In today's fast-paced business environment, speed is crucial. A plastic prototype manufacturer can significantly shorten the product development cycle. Techniques such as 3D printing and injection molding allow for rapid prototyping, enabling businesses to:
- Accelerate Design Modifications: Quickly implement changes based on testing and feedback.
- Launch Products Faster: Enter the market ahead of competitors by minimizing lag time in development.
- Test Market Reactions: Obtain consumer feedback before full-scale production, ensuring better alignment with market desires.
3. Enhanced Design Communication
Having a physical prototype helps in visualizing the final product, thereby enhancing communication amongst stakeholders. A plastic prototype manufacturer assists in:
- Bridging Gaps: Prevent miscommunication between designers, engineers, and marketers by providing a clear reference.
- Encouraging Collaboration: Enable teams to work together more effectively by discussing actual products rather than abstract designs.
- Gaining Stakeholder Buy-In: Impress investors and management with physical representations of product ideas.
4. Customization and Flexibility
Every business has unique needs, and a plastic prototype manufacturer can tailor solutions to meet specific requirements. This flexibility includes:
- Material Selection: Choose from a variety of plastics depending on desired durability, cost, and application.
- Design Variations: Easily modify designs to suit changing consumer preferences or technical requirements.
- Scalability: Transition from prototype to production with a manufacturer who understands your vision and can adapt.
Choosing the Right Plastic Prototype Manufacturer
Not all plastic prototype manufacturers are created equal. Here are key factors to consider when selecting the right partner:
1. Experience and Expertise
Look for a manufacturer with a rich portfolio and years of experience in your industry. Their expertise will offer insights and solutions that new manufacturers may lack.
2. Technological Capabilities
Modern prototyping requires advanced technologies. Ensure your chosen manufacturer utilizes state-of-the-art techniques such as:
- 3D printing
- CNC machining
- Injection molding
3. Quality Assurance Processes
Quality must never be compromised. A reputable plastic prototype manufacturer should have stringent quality control measures in place, including:
- Material testing
- Dimensional and functionality checks
- Compliance with industry standards
4. Customer Support and Communication
Choose a manufacturer that emphasizes customer partnerships. Responsive communication ensures that your needs and adjustments are listened to and addressed promptly.
Case Studies: Success Stories of Businesses Utilizing Plastic Prototyping
To understand the real-world impact of working with a plastic prototype manufacturer, consider the following examples:
1. Consumer Electronics Company
A well-known consumer electronics company sought to develop a new line of smart devices. By collaborating with a specialist in plastic prototyping, they developed a prototype within weeks, facilitating consumer testing and securing funding. The resulting product launch exceeded sales expectations, demonstrating the power of effective prototyping.
2. Automotive Industry Innovator
An automotive parts manufacturer faced challenges with an emerging line of components designed for electric vehicles. Engaging a plastic prototype manufacturer allowed them to create parts that could be tested under real-world conditions, resulting in a 30% reduction in production costs and improved product durability.
The Future of Plastic Prototyping
The field of plastic prototyping is ever-evolving, with innovative materials and technologies paving the way for future developments. Here’s what to watch for:
- Biodegradable Plastics: The push for sustainability will lead to increased use of eco-friendly materials in prototyping.
- Advancements in 3D Printing: Enhanced speed and precision in 3D printing technologies will revolutionize prototyping processes.
- Integration of AI and ML: Predictive analytics will inform design decisions, pushing the boundaries of innovation in prototyping.
Conclusion
The role of a plastic prototype manufacturer is vital in the current business landscape. By providing cost-effective, fast, and customized solutions, they empower businesses to innovate and succeed in their respective markets. As technology continues to advance, the contributions of these manufacturers will only become more significant, ensuring that companies can bring their visionary products to market efficiently and effectively. Navigate your path to success by partnering with a leading manufacturer such as DeepMould.net, where expertise meets innovation.